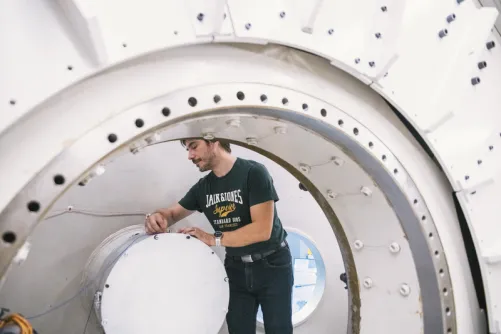
PHARE consists of three test beds
Located on the Centrale Lyon and INSA Lyon sites they bring together experimentalists and numerical engineers.
- PHARE 1: piloted by LTDS, it can accommodate a full-scale aircraft engine rotating under vacuum at real speed to study its vibratory dynamics independently of aerodynamic problems
- PHARE 2:piloted by LMFA, this test rig is specially designed to improve aircraft engine performance from an aerodynamic and aeroacoustic point of view by focusing on fluid/structure coupling
- PHARE 3: piloted by INSA Lyon's LamCoS, PHARE 3 is an on-board structure exciter that enables the influence of external changes to be analyzed
.
Research challenges
- Build predictive and representative numerical tools
- Reduce the energy consumption of rotating machines
- Improve the safety and reliability of equipment (reduce accidental situations such as breakdowns, breakages...)
- Reduce noise pollution
Application areas
- Air transport: new engines, new materials, dissipation, vibration control...
- Power generation: control of vibration levels and extreme situations (loss of blade)
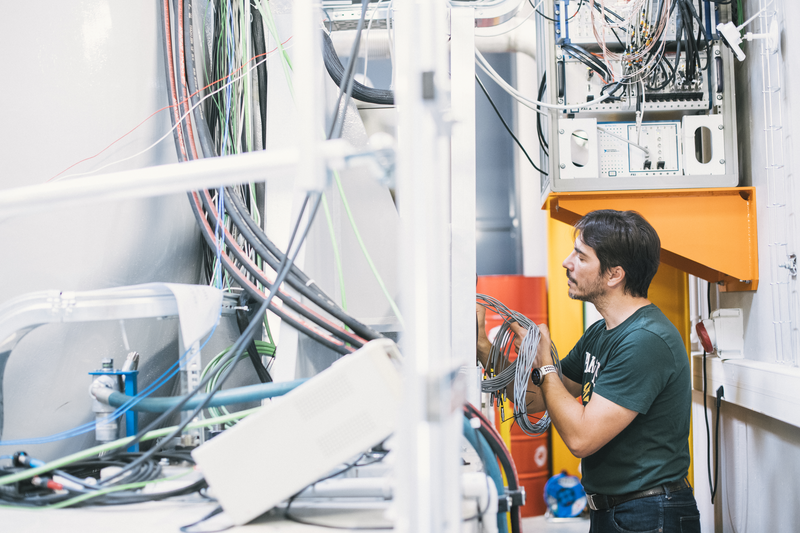
Instrumentation
A large number of sensors are used to measure vibration dynamics and levels of stress, temperature, pressure and speed. The package is completed by fast thermal cameras, image velocimetry to visualize flows (Particle Image Velocimetry - PIV) or non-contact vibration measurement techniques (tip-timing). Components are tested in anechoic and/or primary vacuum chambers at speeds ranging from 0 to 21,000 rpm.